About Windring Hand Made Pottery
Experience
I first met clay in the late 1970s, and have loved it ever since. I trained informally in high-fire porcelain and soon after, with young children at home, set up my own studio. A second-hand kick wheel was joined by a second-hand electric kiln. At that time, considerations of energy use and the practical issues raised by firing pottery in town led me to choose mid-fire clay and electric firing. My special interest was in functional porcelain dinnerware, hand-painted with a cobalt slip in designs of wild grasses, iris, and pine trees.
Many years and workshops later, I practise, experiment, and explore. My wheel is electric, and much quieter! The flow of throwing, and then the creative work of painting and incising designs remain my passions. The bright poppies, lemons, and goldfish designs I am playing with now have their origins in my efforts to bring colour to my pieces during FUSION’s 2016-17 Creative Directions programme. Since then a Kawartha Potters Guild group trip to Korea in 2018 and memories of places near and far, from the Kawarthas and the northern shores of Lake Superior to Portugal and France, have all contributed to influence my work.
An early experience continues to shape my art. As a teen, before my need for glasses was discovered, I saw the night sky stars only as a dim blur; I couldn’t see a person’s expression as they approached; flowers were blobs of colour. Finding form and pattern became key to my understanding the world. Then, suddenly, glasses transformed my world. There was clarity of light, depth, detail, texture. The memory of the first time I saw clearly – saw eyes sparkling and stars twinkling, saw blades of grass and the shapes of leaves – has never left me.
About the Work
Windring pottery is dishwasher and microwave safe. Most is wheel-thrown mid-fire porcelain; all pieces are handmade by me, Priya, in my home studio in Peterborough, Ontario. First versions of some of my current designs appeared in FUSION’s “Unearthed” show at the Robert McLaughlin Gallery, Oshawa, in 2017. My work was among those pieces selected for the most recent 2018 Kawartha Potters Guild juried exhibition at the Art Gallery of Peterborough, and won the KPG award for “Best Functional Pottery in Show” in its last year.
My work is currently available at my home studio, as well as at the Kawartha Potters Guild shop and KPG Holiday and Spring shows, in Peterborough, at Artisanity shows, and at the Gallery on the Lake in Buckhorn.
I appreciate the challenge of creating pieces in various designs, shapes, and sizes to suit different hands, purposes, and preferences. Inquiries and commissions are welcome. My love for clay continues, as does my intent to create pottery that is both functional and a pleasure for the senses.
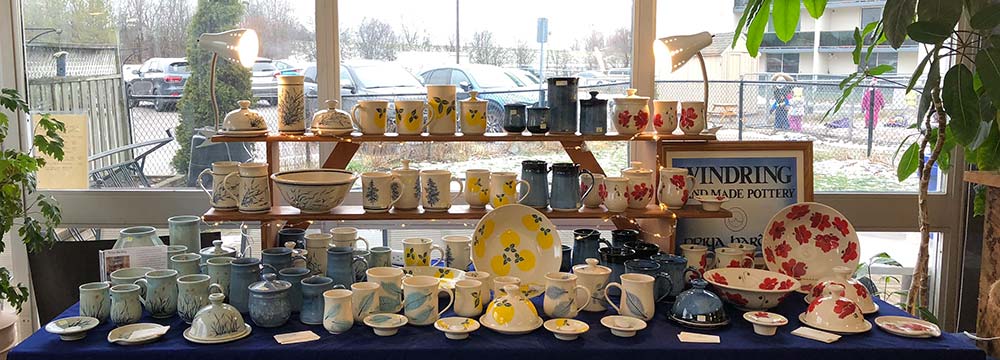
About the Process
The majority of my work is wheel-thrown in cone 6 porcelain, though I occasionally experiment with various mid-fire stoneware clays. Pieces are trimmed when leather-hard, with a good foot ring for curvy mugs, bowls, etc. After trimming, and any additions such as handles, I may add incised or painted designs, depending on my plans for the work, its function, size, and shape. My hand painted designs – the blue grasses, pines, and irises; bright poppies; sunny lemons; koi among water weeds – require a variety of brushes, from liners for grasses and trees, to bamboo for petals, to fine detail brushes for poppy stamens and koi eyes. I prepare the coloured slips with stains or ceramic elements, mixed with clay. When pieces are sufficiently dry, I check that their rims and bases are smooth, then load the kiln for a slow bisque firing to cone 05. Once cool enough to handle, I wash the pieces as I unload, to remove dust, then wax their bases and glaze. Painted work receives a clear glaze for a bright, durable finish; other pieces are frequently glazed in layers, to create a depth and variety of colour. A final turn in the kiln up to cone 6 and then a slow firing down complete the making process.